Sam “King of the Hilltop”
Last time, we talked about considering the costs of manufacturing when planning and designing your board game. If you haven’t read it yet, see the link below. It’s something to keep in mind, especially if you are going to pitch games to publishers. Let them know you are thinking about the production of the game and want to help them be successful as a business.
https://bagamesco.com/2020/01/taking-command-of-board-game-manufacturing/
Now, the next major step is quoting. I highly recommend that you go out there and experience it for yourself. However, if you would like a primer, Panda Game Manufacturing and Starry Games gave me permission to use their quote sheets to help people understand the quoting process for board game manufacturing.
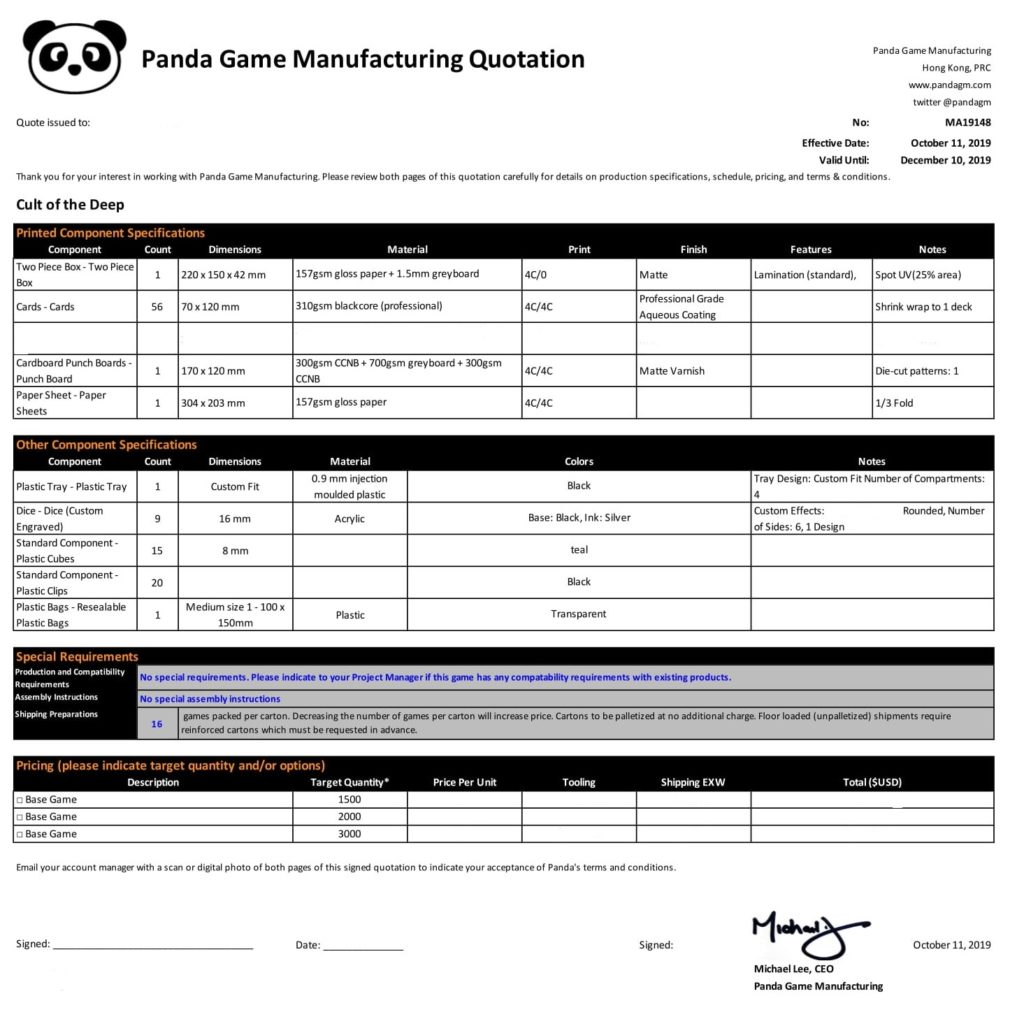
So a few things to notice when working with paper products:
1) When working with “paper” components, this would include the board game box, cardboard tokens, game boards, and anything else that is made of card or paper. They will usually use greyboard. If you have played board games, you have seen it. The sides of tokens have that greyish color. That’s greyboard.
2) Greyboard can be measured in thickness like mentioned above, 1.5mm. The other way is gsm, which stands for grams per square meter. It’s a way to measure paper. Usually, the higher the gsm or density of the paper, the higher the quality. It feels heavier, it doesn’t bend as much, it maintains its shape better.
3) Greyboard is not usually printed on, so where you see something like “300 gsm CCNB + 700 gsm grey board+ 300 gsm CCNB,” the 300 gsm sections are referring to a paper covering over the greyboard.
4) When working with cards, there are a variety of “cores.” This refers to the material that is sandwiched between the two pieces of paper. These cores are what provides the mainstay of how resilient the cards are and their snapback qualities. Meaning when you bend it, does it go back to its original shape. There are a lot of different cores ranging from blue, black, ivory, and even some with none. Even within those cores, they will have quality differences. The higher the cost, they better and stiffer the snap back is. Better quality cards tend to have higher gsm and more resilient cores.
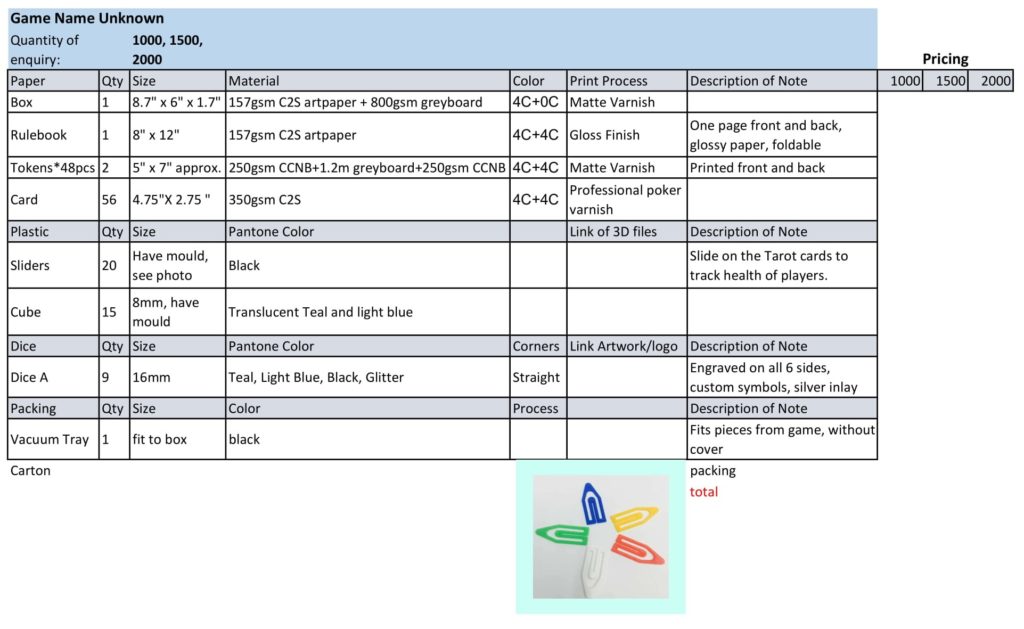
Above is an example of a quote sheet from Starry Games. Let’s take a look at the plastic and dice components.
1) Many plastic components are made from moulds. If a factory does not have a mould to make your item, they will need to make one. This will lead to what is called a tooling cost. If you can use a mould that is pre-existing, this will allow you to minimize that cost and make your product cheaper. The more custom, the more expensive. In the example, Starry Games notes that they already have pre-existing moulds for some of my components. That’s a win!
2) Dice have a similar situation, though there are way more options. You can have different materials like: wood, urea, acrylic, and resin. Each have their own costs associated and uses. Then within those options, you have further options of colors, various layers, additives like glitter, mice, ducks, you name it, you can likely put it in dice. Many board games tend towards simpler dice but remember, the sky is the limit for dice design, but so is their price, so be careful.
There is so much more that goes into quoting and manufacturing a board game than can be contained within a single blog post, or even 2 blog posts. We will definitely cover more, especially since Longpack, who makes a lot of Kickstarter games, gave me permission to use their quote sheet as well. Until next time, go get those board game quotes!
References for Panda Game
Website: pandagm.com Facebook: https://www.facebook.com/pandagm/
References for Starry Games
Website: www.starrygames.com Facebook: https://www.facebook.com/StarryGamesHK/
It’s all about that DICE
Ed “Duke of BAzlandia”
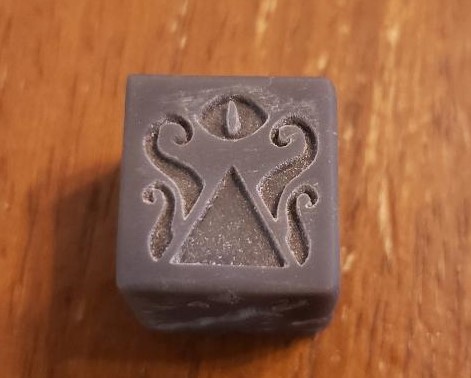
Last time we talked about manufacturing, I talked a little bit about 3D printing. I am not going to go over the same material but I thought, let’s share a project I am working on – dice. Our game Cult of the Deep has dice as a component. In doing some research about game components, I have discovered something, dice are a thing. I remember growing up, playing DnD and have a very meager and small dice collection. I had my favorites within the collection but I had no idea how deep the caverns of the Dice Goblins were and the vast hordes of clik claks they posses. This surprised me.
Cult of the Deep requires a six sided die with a custom symbol for each side. For playtesting, we have used dice with stickers on them. We are curious however how they would look with the sides actually engraved. Luckily, this is where I have a resin 3D printer that will allow me to print the dice with the symbols on the side already engraved. I can print a master die with the resin and use this to make a mold or molds to self cast our own custom die out of resin. If I am feeling ambitious I can even color the resin and do all kinds of things. I have never actually cast any dice before but I have done some casting (Hirst Arts molds).
I am currently in the middle of this process. I have recently moved my resin printer and it has been a pain in getting the die to turn out to where I am happy enough to use it as a master to create the mold and the rest of the dice. I will update as I make progress. Below, you will find a few places I went for research and Hirst Arts just because they are awesome.
https://www.reddit.com/r/ResinCasting/
For monthly Updates enter your email below